Leading the way through innovation...
Advanced Stacking Technology strives to maintain a culture of creativity where thinking outside of the box is the norm. We've developed dozens of ideas over the years that reflect our ability to go where few others have traveled. Below we've highlighted emerging proprietary concepts from AST that are positioned to impact the mining industry in a big way
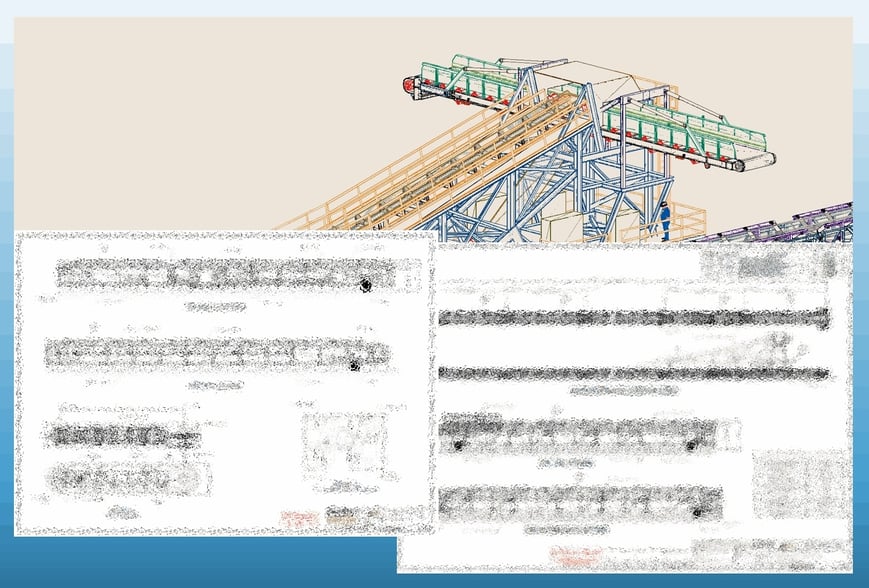
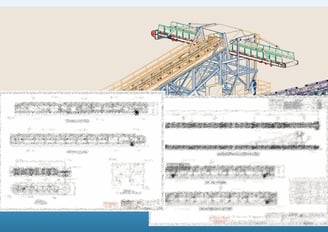
Protected Technology
Crawler Mounted Conveyors (CMC's)
Having two and a half decades of experience designing, fabricating, and supplying mobile belt conveyors, talented AST team members are currently developing a creative new proprietary design for a Crawler Mounted Conveyor that is destined to revolutionize the concept of traversable belt conveyors
Conventional mobile belt conveyors have been around for more than forty-five years. But our state-of-the-art CMC’s cost less, weigh less, are more efficient, and more versatile than their predecessors. This innovative product line is strategically positioned to open a way into an exciting new era of material placement for wet, dry, and blended material handling operations. Since our CMC's are being developed by many of the same people responsible for supplying a majority of the existing mobile conveyors installed worldwide, future placed CMC’s will share the same positive reputation for operational efficiency, reliability, and availability as their forerunners
Traveling Tails Discharge Systems (TTD's)
AST has discovered an innovative method for strategic placement of wet tailings using a mobile placement system called a Traveling Tails Discharge machine. Using proprietary methods, the mobile pipeline system is able to receive tailings, transport them overland, and deposit them lineally using a controlled traveling discharge means. Transported tailings used within the system can either be conventional fluid tailings or thickened tailings, as long as the piped waste contents remain pumpable through the system. Tailings thickening processes are 75% as effective as filter press de-watering methods.
The advantages of a moving discharge system are numerous! Tailings layers can be placed almost anywhere and held to prescribed depths. This allows the pasty tailings by-product to be deposited in large open areas either for atmospheric drying, or as may be desired in other applications, for coordinated blending with dry waste stacking operations.
This breakthrough technology eliminates the need for conventional wet tailings impoundments at many mine sites by bringing multiple waste streams together into single-footprint integrated waste piles. It allows mines to recover process water for reuse or recirculation, at the same time reducing process costs associated with drying of tailings. Use of an integrated waste storage approach can lessen total onsite waste management area needed. It may also shorten duration of land reuse and reclamation efforts required at the end of the mine's life. These are all major wins for today's mining operations!
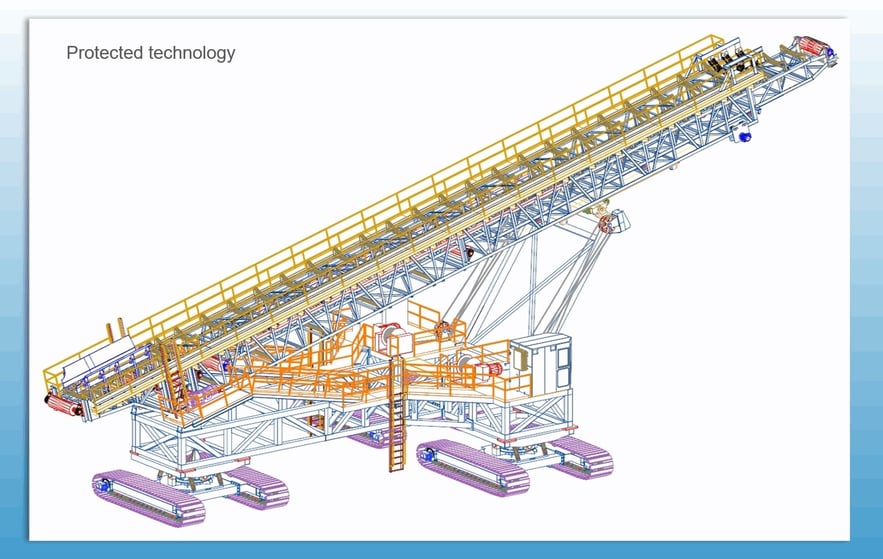
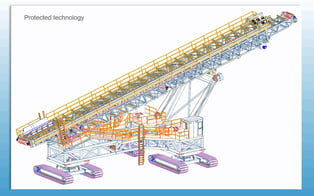
Low GBP Stackers
For the purpose of stacking softer materials, AST has developed a concept for a Low GBP (ground bearing pressure) Stacker. As currently designed, this specialty stacker is able to convey and discharge materials at a rate of 2500 tph, but remains scalable to larger capacities if needed. It has an extendable internal conveyor fame, called a stinger, that reaches an additional 12 meters beyond its fully retracted 41-meter pulley to pulley length. The stacker has an adjustable incline conveying angle of 0 to 18 degrees and is supported on three carbody crawler sets each meeting ground bearing pressure requirements of 7 psi.
By pairing this multi-directional discharging machine with other innovative low GBP material handling systems from AST, such as CMC's, customers are able to economically and securely traverse less than ideal supportive stacking materials like tailings and moist overburden using both advance stacking and retreat stacking material placement methods. Use benefits are significant since they include successful execution of material placement activities which might otherwise be considered unattainable.
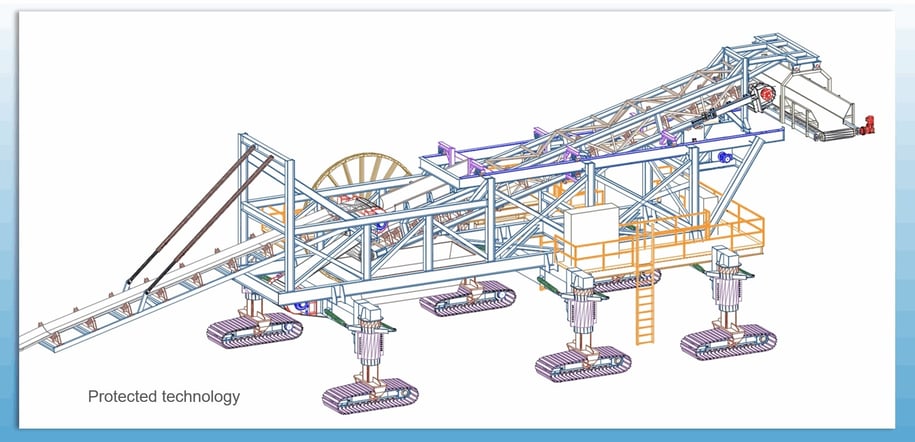
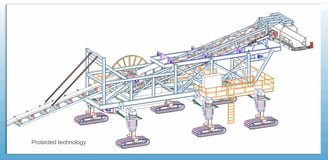
Low GBP Bypass Trippers
AST is currently developing an innovative new concept for a straddling Bypass Tripper. The unique multi-directional low ground bearing pressure (GBP) Bypass Tripper will operate in an integral fashion with the belt of a Crawler Mounted Conveyor (CMC) receiving and placing belt-conveyed material along the length of the CMC, or optionally, directing such belt-moved material through the Bypass Tripper frame and back to the originating conveyor belt for feeding devices downstream.
Development of a Low GBP Bypass Tripper opens up a linear multi-machine end-to-end series arrangement for CMC's that otherwise would not exist. When stacking applications call for exceptionally long CMC's, that is, in excess of 1000 meters (or one kilometer) in length, CMC machines can be configured to transfer material from one to another in a single-line moveable interacting series. The beauty of the arrangement is that it facilitates the formation of a single-acting mobile conveying system having nearly unlimited length. Tired of interrupted production caused by stacking system teardown and relocation activities? Need a 5 kilometer long mobile stacking system? We've got the solution!
Today's CMC's are surprisingly affordable having a price tag that rivals a shiftable conveyor rather than a conventional mobile bridge conveyor. The low GBP Bypass Tripper and low GBP CMC make operationally efficient placement tools for soft material applications such as tailings and moist overburden. Once again, AST has positioned itself to provide and support stacking systems for the next generation that are better for the environment and more cost-effective to maintain and operate.
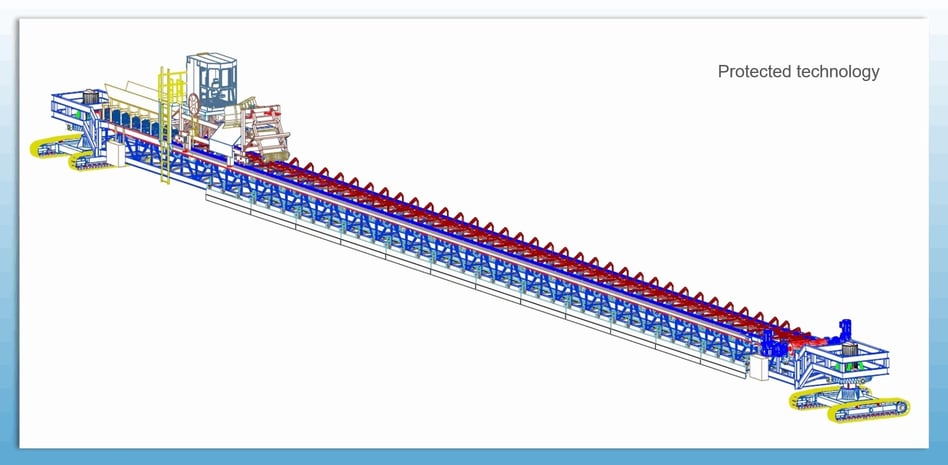
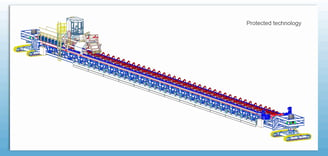
Earth Spreaders
Customers sometimes need the ability to spread thin layers of dirt, mining waste, or gravel. Thin material placement can be required for mine tailings drying applications or earthen structures construction projects. For such tasks as these, AST has developed a concept for an earthen materials placement machine called an Earth Spreader.
Earth Spreaders place a variety of materials in thin placement lifts minimizing the need for dozing and grading equipment by screeding off the top of a low profile 50-meter-wide material discharge trail employing an adjustable blade attached to its lower frame. This combination of advancing machine movement and material strike-off, leaves behind a meter or less of smooth-topped continuous material having a flat surface ready for compaction operations if required. An Earth Spreader has a capacity of up to 2000 tph and significantly reduces time and costs normally associated with thin layer material placement operations and earthen structures construction.

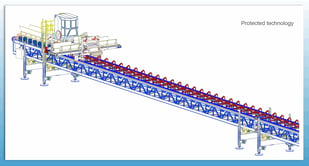
Climbing Conveyors
AST has developed a concept for use in applications where customers need to maintain supply conveyors on top of piles while the piles beneath them progressively grow upward. This inventive machine we call a Climbing Conveyor.
Climbing Conveyors allow customers a continuous method for repositioning feed conveyors so they remain on top of active piles without needing to move such conveyor structures from one material lift elevation to the next. Climbing Conveyors are supported every 50 meters by automated adjustable legs. As a pile grows incrementally in height around a Climbing Conveyor, its leg-pairs are activated to grow in length keeping the conveyor structure at a constant optimal relationship with the pile surface below. As needed, leg-pairs are retracted (raised upward), and available pile backfill materials are pushed below the legs' feet using earth-moving equipment allowing the legs to reset to their minimum extended positions. Leg length adjustment processes and backfilling operations are repeated as necessary to create a "floating" with the pile surface effect for this conveyor.
Climbing Conveyors can be advantageously used where customers desire to reduce expenses and downtime associated with relocation movements of stationary conveyors in dynamically changing pile height applications. Usage examples include long and narrow peninsula-shaped pile stacking tasks where Climbing Conveyors feed mobile stacking systems used to build slender piles sometimes referred to as finger-building operations. Another example is when stacking takes place in a racetrack configuration. In this case, a Climbing Conveyor may be used as the central feed conveyor supplying material to adjacent mobile stacking systems whose lateral laps around the central Climbing Conveyor progressively add new material levels to the top of the pile. In both of these examples, the surrounding stacking activity would eventually bury the feed conveyors unless they're given ability to elevate themselves.
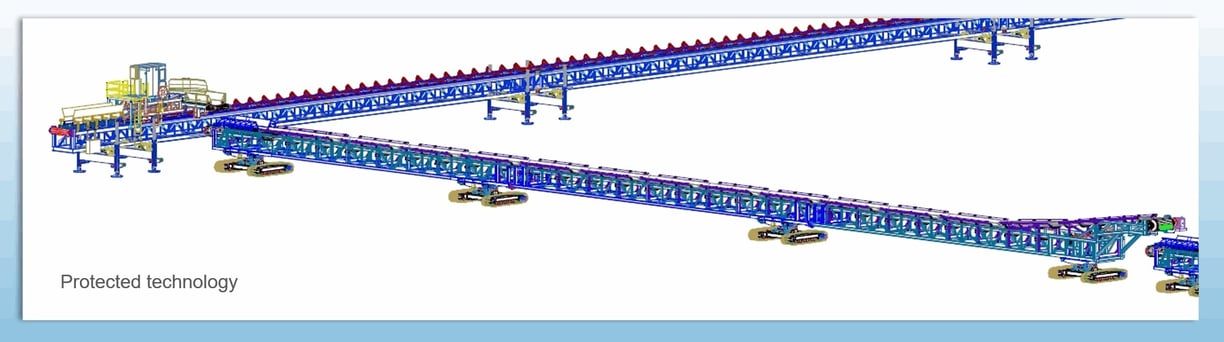
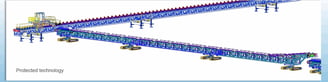
Link Conveyors
The transfer of bulk materials from stationary feed conveyors to mobile placement machines often requires the use of a mobile connecting device called a Link Conveyor. AST has developed a unique concept for a Link Conveyor that improves machine weight and versatility when compared with similar equipment of the past.
Link Conveyors can be designed to fit most any stacking capacity. They range between 50 to 100 meters in length depending on site requirements. Link Conveyors are supported on multiple carbody track sets that allow them to travel in a multi-directional manner enabling them to transfer materials to other moving equipment such as Earth Spreaders, Low GBP Stackers, or other Link Conveyors.
Our unique frame design results in Link Conveyors that weigh less than their conventional predecessors. Reduced machine weight creates advantages when such machines operate within low ground bearing pressure environments. Less weight also results in lower machine costs making AST's innovative product a price standout within a competitive marketplace.